Engine endfloat HELP PLEASE!!!!
psimitar - April 24th, 2012 at 12:54 AM
Hiya,
So I have a very interesting endfloat problem.
I rebuilt the 1200 engine that came with my Beetle last year and as I was in a bit of a rush didn't notice the endfloat problem that will follow.
Fortunately the engine never started 
So take a look at the below picture of the crank installed in the case.
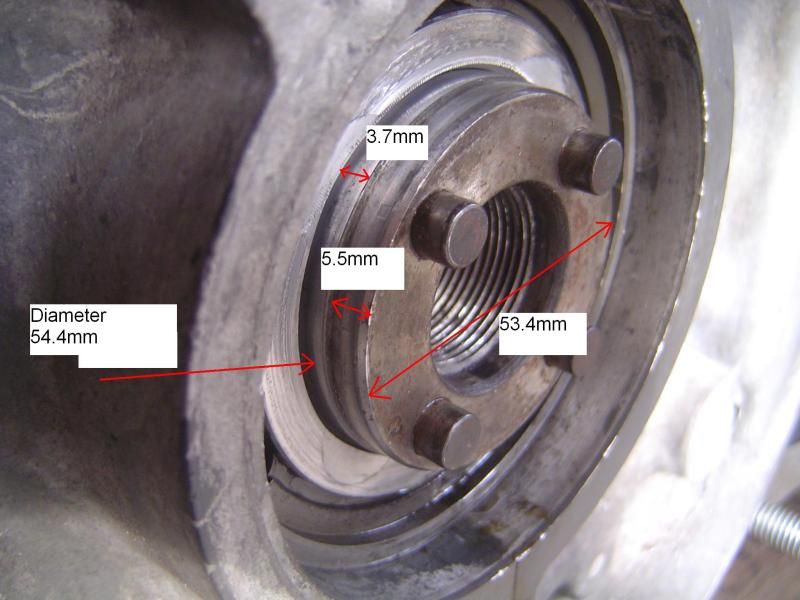
So hopefully the numbers are visable but as you can see the no1 crank journal extends 3.7mm from the thrust bearing face and the journal is
approximately 54.4mm in diameter.
Then the smaller diameter nose of the crank is 53.4mm and is 5.5mm long from the step down from the journal diameter.
The flywheel boss is 8mm deep and has a small change is diameter 4mm into the 8mm crank nose hole.
Right. So can anyone explain to me why my crank is like this because the currently available shims only have an ID of 53.75mm or maybe close to 54mm
but obviously not enough to fit over the crank journal that extends for the thrust bearing and be able to sit flush against the thrust bearing
face.
I'm wondering if there was some kind of intermediate engine changes from the early 1100 and 1200 cranks with 48mm endfloat shims to the later 53.75mm
shims of all other T1 engines?
What with the step in the flywheel and the crank nose lining up it's almost like an 'O' ring used to squish up in here and that journal sized ID
shims where used.
Please, please, please can anyone help me in figuring this out cos at the moment the only option I can think of is having the crank nose ground so
that the 53.4mm nose extends back to just inside the thrust bearing and therefore allowing the later shims to fit correctly.
If you're wondering with the flywheel fitted up I have roughly 1mm of endfloat but this is without the metal or paper gasket fitted to the end of the
crank nose.
HELP!!!!!!!!!!!!!!!!!!!!!!!!!!!!!
dangerous - April 24th, 2012 at 05:16 AM
Yes, the early cranks used shims with a larger diameter to fit over the journal just as you say.
They did not use an O-ring, but did use a gasket on the end of the crank to stop the oil from getting out past the dowels.
You need to make sure that the bearing is not moving within the case, thus giving you a false reading.
matberry - April 24th, 2012 at 07:52 AM
6volt crank needing 6volt end float shims.
psimitar - April 24th, 2012 at 11:19 AM
Bearing is brand new and machined to fit the case nice and snuggly. so the bearing is not moving around.
I know the earlier cranks use a gasket on the end, thats not a problem.
As for these 6V shims. They must be a part that was used between the early engine with 48mm ID shims and the later 12v shims but I can't seem to find
a supplier anywhere in the world. There's one guy in the UK who is the sole supplier of the early 48mm shims and then everyone else just has in stock
the later 53.75mm ID 12v shims.
So if these 6v shims ever did exist, any idea's where to get em?
Otherwise I'll have to get the crank ground up by the thrust bearing to the smaller diameter of the 12v shims (66 onwards)
matberry - April 24th, 2012 at 01:38 PM
I only have a stash of second hand 6 volt shims. Grinding the crank down is a fix but I believe a O-ring flywheel should then be used.
psimitar - April 24th, 2012 at 07:42 PM
Quote: |
Originally
posted by matberry
I only have a stash of second hand 6 volt shims. Grinding the crank down is a fix but I believe a O-ring flywheel should then be used.
|
Matt, could you measure the ID of your shims to see if they would actually fit this crank of mine?
As for the 12v flywheel I believe the 6v will be OK with a new end gasket as it's just stopping oil from making its way into the gland nut thread and
does the same job as the 'o' ring
matberry - April 24th, 2012 at 09:56 PM
Sorry mate, have checked all of my shims and only 12V, type 4 and 36hp.....no 6V unfortunately. Some one here will have some. Or try Vintage Vee Dub.
psimitar - April 24th, 2012 at 10:20 PM
Quote: |
Originally
posted by matberry
Sorry mate, have checked all of my shims and only 12V, type 4 and 36hp.....no 6V unfortunately. Some one here will have some. Or try Vintage Vee Dub.
|
Cheers for looking Matt 
Are you pretty certain that the 6v shims will fit? I'll call Vintage tomoro and ask them to check for me but if you're still online thought I'd ask
you first
Cheers,
Mike
matberry - April 24th, 2012 at 10:59 PM
Yep, shims to suit the earlier 6 volt crank, all 40hp and some 1500 type 3 (among others no doubt). Holiday tomorrow, but you'll have them by the
weekend if you call on thursday morning.
matberry - April 24th, 2012 at 11:01 PM
I'd measure up your end float dry, no oil, no shims. And try for a stack the correct size. Must measure accurately though
psimitar - April 25th, 2012 at 03:20 PM
Quote: |
Originally
posted by matberry
I'd measure up your end float dry, no oil, no shims. And try for a stack the correct size. Must measure accurately though
|
Yea I used the digital vernier the other day and it said 1.03mm but I have a 0.01 increment 10mm dial guage that I just need to make a stand for.
Think I may just use the paper end gasket instaed of the metal one as I don't like the way the metal gasket sits and has formed some nasty lips on
the edges.
Old Dubber - April 25th, 2012 at 05:28 PM
I have some second hand 6 volt shims
psimitar - April 25th, 2012 at 09:59 PM
Quote: |
Originally
posted by Old Dubber
I have some second hand 6 volt shims
|
Cheers Grahame
I'll see what vintage have new as there is always a
little bit of wear on old shims but if that falls thro I'll give you a call
matberry - April 25th, 2012 at 10:38 PM
I would use the metal gasket but clean it up with sandpaper on glass. The paper gaskets collapse over time. Vernier isn't accurate enough for
endfloat adjustment, but your dial indicator is the go.
psimitar - April 26th, 2012 at 12:04 PM
Quote: |
Originally
posted by matberry
I would use the metal gasket but clean it up with sandpaper on glass. The paper gaskets collapse over time. Vernier isn't accurate enough for
endfloat adjustment, but your dial indicator is the go.
|
Yea, think I'll reuse the old metal one cos its in much better condition than the 2 new ones I have. Just need a bit of glass now
and a block of ali to make the gauge stand from
HappyDaze - April 26th, 2012 at 12:15 PM
I remember seeing Jack Bono lapping a flywheel onto a crank, with valve-grinding paste.He would not use the paper gaskets, and made his own metal
gaskets [when only paper ones were available] from aluminium ice-cream containers.
matberry - April 26th, 2012 at 01:00 PM
Quote: |
Originally
posted by HappyDaze
I remember seeing Jack Bono lapping a flywheel onto a crank, with valve-grinding paste.He would not use the paper gaskets, and made his own metal
gaskets [when only paper ones were available] from aluminium ice-cream containers.
|
Yeah, 8 dowels get pretty tricky....
hellbugged - April 26th, 2012 at 02:20 PM
I have the hellbug box of shims at home at the moment and can look for what you need
HappyDaze - April 26th, 2012 at 03:22 PM
Quote: |
Originally
posted by matberry
Quote: | Originally
posted by HappyDaze
I remember seeing Jack Bono lapping a flywheel onto a crank, with valve-grinding paste.He would not use the paper gaskets, and made his own metal
gaskets [when only paper ones were available] from aluminium ice-cream containers.
| Yeah, 8 dowels get pretty tricky....
|
Tricky, yes.....impossible, no. In 1961, when Jack built my [40hp] engine, the paper gasket collapsed very quickly. Merv Waggott '8 dowelled ' the
crank & f/wheel, and as you say, making the al. gasket was pretty tricky - I know, because I got the job! A pair of nail scissors and a
ball-bearing were the main tools. There was no alternative, as the paper gasket was the only thing available.
psimitar - April 26th, 2012 at 03:42 PM
cheers guys. Vintage have a stack of used shims. No one makes new ones anymore.
So I'll measure over the weekend and then see who can help with the sizes I need. Willing to pay if needed of course cos Vintage weren't exactly
gonna give em away now were they 
dangerous - April 27th, 2012 at 06:09 PM
I have some NOS "6Volt" shims.
Let me know what sizes you will need, and I might be able to help.
...but you are correct, they are not inexpensive.
psimitar - April 27th, 2012 at 10:52 PM
Quote: |
Originally
posted by dangerous
I have some NOS "6Volt" shims.
Let me know what sizes you will need, and I might be able to help.
...but you are correct, they are not inexpensive.
|
Cheers dude,
Yea Vintage said a tenner each used but when they used to get em new they were $18 each. Ouch!!! At that price almost cheaper to get the nose reground
for 12v shims
dangerous - April 28th, 2012 at 05:09 AM
I normally charge a tenner each for the NOS ones when I do an engine end float assembly.
Plus a tenner for postage.
psimitar - April 28th, 2012 at 12:36 PM
Quote: |
Originally
posted by dangerous
I normally charge a tenner each for the NOS ones when I do an engine end float assembly.
Plus a tenner for postage.
|
Very Reasonable kind sir
Hopefully I'll get to measure them today or
tomoro and let you know what I have
psimitar - April 29th, 2012 at 06:45 PM
So I measured the endfloat today and ended up with the following.
With metal end gasket = 1.26mm
Without metal end gasket = 1.04mm
So with the metal gasket and using 3 of the thickest shims, at 0.36mm, then this gives 1.08mm plus the 0.1mm endfloat gap gives 1.18mm. So not enough
and the 0.08mm takes me outside the allowed tolerance.
Without the gasket and minus the endfloat gap I get 0.98mm. Divide by 3 and we get 0.3266666666mm or 2x 0.32mm and 1x 0.34mm. So that works.
I'm wondering if I can find an 'O' ring that may fit without machining the flywheel. Otherwise I can either get the flywheel machined for an 'O'
ring or take the engine apart to have 0.2mm machined from the crank nose.
Ideas anyone?
matberry - April 29th, 2012 at 09:40 PM
Yes, you can machine the lip of an O-ring flywheel to fit. No problem.
psimitar - April 29th, 2012 at 09:59 PM
Quote: |
Originally
posted by matberry
Yes, you can machine the lip of an O-ring flywheel to fit. No problem.
|
Does it have to be an 'O' ring flywheel, i.e. a later 120 tooth wheel and not a 109 tooth wheel?
If I have to get a 12v wheel then that means I'll need flywheel, starter and 200mm clutch. Now thats a fricking nuisance for 0.2mm
Attached is a sketch of the layout of the crank nose and flywheel. The red circle is the possible placement of a 54mm 'O' ring 2mm thick to plug the
gap. The very end of the crank nose and flywheel have maybe 0.1mm clearance but the other area is 54.5mm on the crank and 57mm in the Flywheel. Or
have a channel machined in the flywheel for an O ring? What do you think?
matberry - April 29th, 2012 at 10:25 PM
Ok, yes your right, it would be an O-ring flywheel therefore the majority are 130 teeth '12-Volt' not 109 teeth '6-Volt'. They are rare, but I
have seen 6 volt O-ring 180mm from a Euro standard '69. Maybe Dangerous could perform the tricky job of machining an O-ring groove into your 6-volt
flywheel.
psimitar - April 29th, 2012 at 10:43 PM
Quote: |
Originally
posted by matberry
Ok, yes your right, it would be an O-ring flywheel therefore the majority are 130 teeth '12-Volt' not 109 teeth '6-Volt'. They are rare, but I
have seen 6 volt O-ring 180mm from a Euro standard '69. Maybe Dangerous could perform the tricky job of machining an O-ring groove into your 6-volt
flywheel.
|
oh you replied whilst I was messing about with Paint for the attachment.
Any machine shop should be able to machine the groove I woulda thought? Would require a specially ground 90 degree chamfer tool tho
psimitar - April 30th, 2012 at 07:01 PM
Quote: |
Originally
posted by matberry
Ok, yes your right, it would be an O-ring flywheel therefore the majority are 130 teeth '12-Volt' not 109 teeth '6-Volt'. They are rare, but I
have seen 6 volt O-ring 180mm from a Euro standard '69. Maybe Dangerous could perform the tricky job of machining an O-ring groove into your 6-volt
flywheel.
|
Righto, so off to Micks tomoro for a new seal and O ring and then off to Brendale and see if my old machinist can groove the flywheel for me