[ Total Views: 6624 | Total Replies: 72 | Thread Id: 97354 ] |
Pages: 1 2 3 |
|
empi
A.k.a.: Empstar
Compulsive Aussie Vee Dubber
     
Posts: 4131
Threads: 178
Registered: August 27th, 2002
Member Is Offline
Location: melbourne
Theme: UltimaBB Pro Blue ( Default )
Mood: thunderous
|
posted on June 19th, 2012 at 10:53 AM |
|
|
316 =1966
Will consult my australian type 3 colour brochure... back soon
"If at first you don't succeed, skydiving is not for you." - Anonymous 
|
|
eXraycer
Seriously Crusin Dubber

Posts: 166
Threads: 27
Registered: May 16th, 2012
Member Is Offline
Theme: UltimaBB Pro Blue ( Default )
|
posted on June 22nd, 2012 at 09:37 PM |
|
|
Quote: | Originally
posted by empi
316 =1966
Will consult my australian type 3 colour brochure... back soon
|
How did you go with that?
Currently I'm almost certain it's an Aussie built or at least Aussie assembled car. And most likely Bahama Blue although the colour number sticker
is long since gone..
Still trying to determine this cars origin or find out all I can about it. Whether it was completely made in Australia or assembled here from a CKD
(Complete knock Down) or a combination of import and locally made parts. The interior looks original and in Brown colour. Vertical stitch lines but
no perforations or two tone colours for the interior. Z shaped front arm rests. One of which is missing, drivers side. (If anyone has one to spare I
would be interested in purchasing it from you).
The car might be sporting German made glass from the german sounding inscriptions but i will take a pic. (Will take more pics of the markings and
dash and door tops on the weekend) although no rear pop outs on this car again suggesting Aussie made vehicle if i'm not mistaken.
I thought the glass was made locally on the Aussie made cars??? but I guess in those days they probably did whatever they had to in order to fill the
quota or meet the demand.
Found the Body number plate in the spare wheel location suggesting that it might have been assembled in Australia from what I've read here on
Aussieveedubbers. Is that true for 1966? Is is possibly a CKD kit or completely made here. How would I be able to tell the difference? or have I got
enough information already to work that out?????
Chassis and Compliance plate numbers match. Definitely 66 model. (316XXX)
Zenith blue is looking less likely - am I right in saying that?
|
|
Burrelli
Officially Full-On Dubber
 
Posts: 244
Threads: 4
Registered: October 12th, 2008
Member Is Offline
Theme: UltimaBB Pro Blue ( Default )
|
posted on June 22nd, 2012 at 10:29 PM |
|
|
TS fastbacks are Australia only and have panels pressed in Australia not CKD. They still have "Made in Germany" on the tag because not enough of the
car was made in Australia to say that.
It will have mostly Australian glass.
Interiors where Australian.
Tail light lenses, starter motor, gennie say made in Australia.( lost of other part as well. Even later CKD cars had lots of Australian parts)
If it was a German 66 fasty it would have disc brakes and would have a TL badge and all German parts.
|
|
eXraycer
Seriously Crusin Dubber

Posts: 166
Threads: 27
Registered: May 16th, 2012
Member Is Offline
Theme: UltimaBB Pro Blue ( Default )
|
posted on June 22nd, 2012 at 11:55 PM |
|
|
Thanks a lot for the clarification. Just the sort of info I was looking for.
Can anyone confirm the Aussie fastback colours for 66?
The light blue oxidised paint exterior takes on a warmer light green hue in the areas with less paint oxidation. I'm gonna hit a test patch with
polish I think. From descriptions I've read about Bahama blue it sounds very similar.
2c anyone??
|
|
67fasty
Casual Dubber
Posts: 31
Threads: 9
Registered: May 23rd, 2006
Member Is Offline
Theme: UltimaBB Pro Blue ( Default )
|
posted on June 23rd, 2012 at 06:57 PM |
|
|
I agree with Empi's earlier post - looks Zenith to me.
As Dean from the Curiousity Show used to say..."here's one I prepared earlier":
|
|
eXraycer
Seriously Crusin Dubber

Posts: 166
Threads: 27
Registered: May 16th, 2012
Member Is Offline
Theme: UltimaBB Pro Blue ( Default )
|
posted on July 7th, 2012 at 12:45 AM |
|
|
OK, finally I've had confirmation and its definitely Bahama blue so I have updated the thread title. Was confirmed by two experts in the flesh both
of which have owned Bahama blue vw's.
Anyhow there's been some progress. Pulled out and panel beated the front beaver. I found an old school panel beater who wasn't scared of a few hours
solid work. Together we pushed out the beaver using the car jack against the front beam to stretch it. then more than a few solid hits and some hammer
and dolly work and she's nearly done. a bit more work to do but the shape is looking good.

Now some more work required on the front right light bucket damage and a little rust repair required under the back left tail light. Oh and the rear
beaver is a bit bent too. Hey it was a Bathurst car. Probably ran over a wombat or a stump in a paddock at some stage and pulled out the rear beaver.

|
|
eXraycer
Seriously Crusin Dubber

Posts: 166
Threads: 27
Registered: May 16th, 2012
Member Is Offline
Theme: UltimaBB Pro Blue ( Default )
|
posted on July 11th, 2012 at 09:45 PM |
|
|
Some more panel repairs.
Here - the light bucket damage. Odd spot for isolated damage. Took some oxy heat and some more panrl beating.

Here some rust repairs. replacing the hard to fix area with part of an easier to fix panel. The lesser of two evils I guess. Couldn't really find a
perfect panel to fix it with so we fitted the slightly better green section then fixed a little bit of rust that was in that peice.

|
|
eXraycer
Seriously Crusin Dubber

Posts: 166
Threads: 27
Registered: May 16th, 2012
Member Is Offline
Theme: UltimaBB Pro Blue ( Default )
|
posted on August 5th, 2012 at 09:26 PM |
|
|
Slow going but I managed to drop the engine, gut the interior and separate the body from the chassis in the last couple of weeks with the help of a
friend. Would have had more done but I'm also trying to settle in to this new garage I built at work. Making benches, fitting compressed air lines,
shelving and roller door has all slowed me down a lot but I'm ready now to go full steam. Just finishing my body frame so I can remove the chassis
and work on it concurrently. Thinking of doing an IRS conversion, and adjustable rear spring plates. Not sure yet. Will mull it over some more before
I decide.
The engine in my car is quite the paradox. It is rusted and corroded beyond beleif but then you look at the body with only the small amount of rust we
cut out of the rear qtr and a small hole under the front corner of the fuel tank. It is really baffling. But the motor looks like its been under sea
water. Anyhow if you got to know the history. The car was bought from central western NSW. They've gone through a number of field mouse plagues in
the past and the fan housing, air ducts and muffler were litterally full of mouse sh#t and organic matter. My best guess is that the engine was pi$$ed
on by a million hungry mice in their frenzy to find a place called home so they can crap in it. Thank god the interior was locked up and windows shut
tight.
And here is the proof I found on Saturday as I pressure washed that crap off the engine. One dessicated mouse trapped in the engine tins.




Not sure if this is gonna work. I thought I'd improvise and make a car body wheelable frame to sit it on whilst I work on the chassis. I Have since
bolted the orange crossmembers to the uprights to give it more stability and will put a third u bolt on each corner of the blue crossbars for
redundancy. Supercheap were having a sale on trailer hitch wheels at $20 each which I thought was pretty good. I Wanted to make it without welding.
Also to save cost I used steel and unused racking I had in the warehouse. I think the pallet racking should hold no problem. We put over a tonne on it
in the warehouse.
|
|
L469
Officially Full-On Dubber
 
Posts: 288
Threads: 15
Registered: March 5th, 2010
Member Is Offline
Location: nsw
Theme: UltimaBB Pro Blue ( Default )
|
posted on August 6th, 2012 at 04:21 PM |
|
|
great idea for the rack. loving this thread keep up the great work.
looking forward to the next instalment
|
|
Pfeffernuss
Slammed & Awesome Dubber

Posts: 80
Threads: 16
Registered: March 25th, 2012
Member Is Offline
Location: Canberra
Theme: UltimaBB Pro Charcoal
Mood: retrospective
|
posted on August 6th, 2012 at 09:23 PM |
|
|
This is great, I can be a passenger to this rebuild, whilst I rebuild my '71
Besser als in die hohle Hand geschissen.
'71 Type 3 Fastback
'08 WRX
'14 Golf Variant HL
|
|
eXraycer
Seriously Crusin Dubber

Posts: 166
Threads: 27
Registered: May 16th, 2012
Member Is Offline
Theme: UltimaBB Pro Blue ( Default )
|
posted on August 7th, 2012 at 01:18 AM |
|
|
A little bit more prep work before I lift it. As I'm not sure how strong the A pillars are I thought I should brace up the door openings before I
lift it. Here's the handy work. took bloody hours to fabricate them to a tight fit. The old 'measure twice, cut once rule", worked out for me. They
fit like a glove.


|
|
eXraycer
Seriously Crusin Dubber

Posts: 166
Threads: 27
Registered: May 16th, 2012
Member Is Offline
Theme: UltimaBB Pro Blue ( Default )
|
posted on August 10th, 2012 at 04:03 PM |
|
|
We have lift-off................
After a long cold night we finally dropped it's pants. The frame worked out pretty good. Just fits under my roller door and the chassis will wheel
under the body no probs to give me more room in the garage if I need it.
Here's how we did it. I'm sure everybody will have their own method and it is dependant on the equipment available to you so I'm not saying it's
the only way, just my way.
Wheel the frame into position without the front crossbar attached. Jack the rear of the chassis up as far as you can. Lift the rear of body up a
little more so you can wheel the crossbar of your frame under the chassis mounts at the top of the shock tower. (i'm lucky I had a little mini
forklift but its light enough if you had 3 blokes or if your floor jack had a bit more lift than mine had. Then drop the chassis down. (That's
assuming you've done all the prep works and removed all the chassis bolts and attached wires). You could do it on your own with the right method and
equipment but this sort of job I felt it was good to have at least one other person around.

Next, lift the front up and slide the front crossbar into position. Again we jacked up the chassis most of the way but this time it was easy to
manhandle it and slide the crossbar onto the 'u' bolt cradles I made. You'll note the front crossbar hangs below my orange beams about 150mm lower
than the rear. It gives you a pretty level car this way. I used threaded rod to make the 'u'bolts and used three per corner to give me some
redundancy.

At this point we just dropped the chassis down and wheeled it out.


(Note if anyone decide to make their own frame like this, a word of warning. Add in some high tensile bolts to lock the orange beams to the posts by
drilling through the lot. The normal pins that lock the posts to the beams are dependat on weight. If you happen to wheel the unit around and one
corner becomes un-weighted the leg keyholes will let the leg drop off the beam and your whole thing could topple over. Also with regards to the
trailer hitch wheels, I used 'u' bolts that were not for round posts they were squared 'flat' on th 'u' shape which wanted to squash the
vertical hitch/shaft of the castor wheel and it restricted the ability of the wheel to change direction. If you do something like this you might be
better off to weld some conventional castors to the base of the corner posts. It's a whole lot of mucking around that can be done a lot easier if you
get your hands on a mig welder.)
Here's how I lifted the body up tha last little bit to let me roll the crossbar and frame under but I reckon you could do the same with two men or a
block and tackle or a taller trolley jack. I like having the chassis up under the body only a few inches away for safety until I knew the crossbar was
in the right spot and supporting the body. Probably a little bit of overkill on my part but it was really hard to find a straight car and I'm a
little protective of it.
|
|
eXraycer
Seriously Crusin Dubber

Posts: 166
Threads: 27
Registered: May 16th, 2012
Member Is Offline
Theme: UltimaBB Pro Blue ( Default )
|
posted on September 3rd, 2012 at 10:29 AM |
|
|
Been cleaning up the pan. it's in pretty good condition. One small hole to repair near battery and two other tiny spots where i punched a hole where
I thought it was thin. I will patch them rather than replace with a large pan section cause the pan is sound. At some point in its life somebody saw
surface rust in the battery area and coated the back half with a red rust preventative paint. It surely saved the battery side pan so I got lucky.
Some pics of the stripping. Tried straight sand blasting at 90psi but found an easier workflow was to wire wheel it first with the air grinder then
sandblast with Aluminium oxide.

|
|
eXraycer
Seriously Crusin Dubber

Posts: 166
Threads: 27
Registered: May 16th, 2012
Member Is Offline
Theme: UltimaBB Pro Blue ( Default )
|
posted on April 26th, 2013 at 11:55 AM |
|
|
Time for an update here:
Its been a little slow but I keep taking small steps forward.
Front beam is reconditioned and painted. Ready for assembly. ( leave that for now )
Chassis still up on its side. I left that for now, almost ready for paint on it. Just want to get the rear subframe sorted.
Rear subframe is a project of its own. I'm in the process of installing pivot boxes on the early swing axle subframe in order to go full IRS
suspension.
Judging from the quotes I got I knew it wasn't going to be easy to do so I prepared myself for a hard slog. It's definitely not a fun job but I've
cut no corners so I'm happy with the progress.
Thought I'd be clever and bought aftermarket pivot boxes but I didn't like the angle they attached to the beam at. It meant notching them into the
frame horns a huge amount. So not wanting to cut the frame horns a great deal I opted to cut the pivots off the donor IRS rear end.
Cut the beam then grind them from the rear so there was no loss of metal around the circumference where they attach to the beam.

Must say, this is one of the hard jobs. I hated doing it. Slow, tedious, intricate grinding from an obsessive compulsive meant it took hours. Yuk.
Next was another slow and tedious cut to do. The notch into the frame horn. Measure twice cut once. Unfortunately you also gotta do a little at a time
or you'll end up with a bigger hole than required.
I got it very close to perfect. Happy with the result. One side done after about 2 hours if back and forward cut/test fitting.
Take a template then stick it onto the other side. Second one was a lot quicker.
I used an air cutter. (reciprocating air cutter.) to do the detailed cutting. Best 90 bucks I ever spent. (tip; do not buy the really cheap ryobi air
saws from bunnings. After two units packed it in within 3 minutes I gave up and bought a better quality unit fromTotal tools).





At this point I must tell you about the pivot box jigs.
I borrowed one set from someone i knew that are production items made in USA for bugs but they don't clear the shock towers on a type 3. I was about
to build my own but during a casual conversation with Mike at Vintage Veedub he mentioned that they had a custom made set that would work and are
available for hire.
Sometimes you get lucky. These jigs are awesome. So solid and absolutely spot on when I test fit them into the old donor IRS rear end. So, a big
thanks to Vintage Veedub. Access to these jigs saved me about a whole day of trying to fabricate my own jigs.

I will upload a few more pics soon. Just need to tack it on and think a little more about my Kafer bar setup I'm going to make from chromoly tubing.
Gonna do that too before I give it to a professional to weld up the whole job. I want a frame builder to weld this since its a structural suspension
component.
|
|
empi
A.k.a.: Empstar
Compulsive Aussie Vee Dubber
     
Posts: 4131
Threads: 178
Registered: August 27th, 2002
Member Is Offline
Location: melbourne
Theme: UltimaBB Pro Blue ( Default )
Mood: thunderous
|
posted on April 26th, 2013 at 08:37 PM |
|
|
u should just get a later irs subframe and bolt it in. dont foret the engine hanger mounts on the body.
"If at first you don't succeed, skydiving is not for you." - Anonymous 
|
|
eXraycer
Seriously Crusin Dubber

Posts: 166
Threads: 27
Registered: May 16th, 2012
Member Is Offline
Theme: UltimaBB Pro Blue ( Default )
|
posted on April 26th, 2013 at 10:14 PM |
|
|
Hi Empi,
I was not going to do the rear engine hanger like later models which bolts to the inner guards. Welding mounts to the sheet metal in there just
didn't seem like a solid way to hang a warmed up motor. I thought it might be prone to cracking and warping the inner guard area but I can't say
from experience, just didn't seem like the best way to do it although I'm sure it would have been a lot easier. The whole point of doing the IRS
conversion to the swing axle sub frame with the frame fork design should support the gearbox and motor like an IRS beetle. The Kafer bars (yet to be
made) will further support and minimize the torque effect of the motor on the frame fork.
If you see I already had a later subframe which I bought for parts and pivot boxes.
I had seen a few custom builds like this and chose to follow their lead. Being a bolt in subframe and having another spare swing axle subframe I
bought really cheaply on eBay I felt that the mods are easily reversed if I choose to revert the car back to stock one day.
|
|
matberry
Super Moderator
Go hard or go home
     
Posts: 8114
Threads: 134
Registered: March 7th, 2006
Member Is Offline
Location: Cooroy Qld
Theme: UltimaBB Pro Blue
Mood: enjoying waving at all my Kombi buddies from my T3
|
posted on April 26th, 2013 at 10:38 PM |
|
|
I think you made a good choice. As you said, the body cracks in the rear even with a standard engine.
Great job.
Matt Berry Motorsports...air cooled advice, repairs and mods Ph 0408 704 662
OFF-ROAD,CIRCUIT,DRAG,STREET,ENDURANCE

|
|
vlad01
Compulsive Aussie Vee Dubber
     
Posts: 4270
Threads: 109
Registered: June 3rd, 2010
Member Is Offline
Location: Kyneton, VIC
Theme: UltimaBB Pro Blue ( Default )
Mood: Side ways
|
posted on April 27th, 2013 at 10:11 PM |
|
|
the jigs! awesome. so they are available for hire?
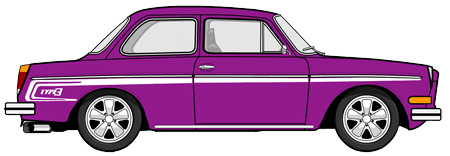
71 notchback,
Past owner of, 70 NB, 73 SB and 72 FB TLE
|
|
vlad01
Compulsive Aussie Vee Dubber
     
Posts: 4270
Threads: 109
Registered: June 3rd, 2010
Member Is Offline
Location: Kyneton, VIC
Theme: UltimaBB Pro Blue ( Default )
Mood: Side ways
|
posted on April 27th, 2013 at 10:14 PM |
|
|
Quote: | Originally
posted by matberry
I think you made a good choice. As you said, the body cracks in the rear even with a standard engine.
Great job.
|
yes thats my experience too and I am going with this same setup plus kafer bars.
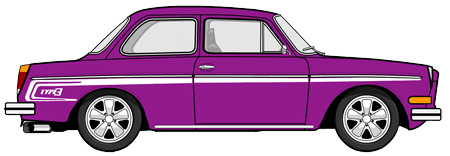
71 notchback,
Past owner of, 70 NB, 73 SB and 72 FB TLE
|
|
empi
A.k.a.: Empstar
Compulsive Aussie Vee Dubber
     
Posts: 4131
Threads: 178
Registered: August 27th, 2002
Member Is Offline
Location: melbourne
Theme: UltimaBB Pro Blue ( Default )
Mood: thunderous
|
posted on April 28th, 2013 at 09:39 AM |
|
|
Make sure yr Cvs clear
"If at first you don't succeed, skydiving is not for you." - Anonymous 
|
|
vlad01
Compulsive Aussie Vee Dubber
     
Posts: 4270
Threads: 109
Registered: June 3rd, 2010
Member Is Offline
Location: Kyneton, VIC
Theme: UltimaBB Pro Blue ( Default )
Mood: Side ways
|
posted on April 28th, 2013 at 10:46 PM |
|
|
Quote: | Originally
posted by empi
Make sure yr Cvs clear
|
good point. Never thought of that when using stock gearbox.
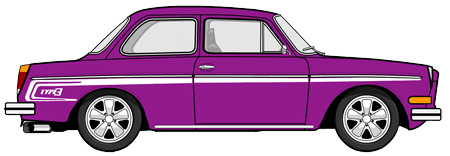
71 notchback,
Past owner of, 70 NB, 73 SB and 72 FB TLE
|
|
eXraycer
Seriously Crusin Dubber

Posts: 166
Threads: 27
Registered: May 16th, 2012
Member Is Offline
Theme: UltimaBB Pro Blue ( Default )
|
posted on April 29th, 2013 at 03:52 PM |
|
|
Quote: | Originally
posted by vlad01
the jigs! awesome. so they are available for hire?
|
Yep for hire, just speak to Mike at vvds. Gimme a couple weeks before you ask for them. I wanna mock up my kafer bars first and then get the whole lot
welded professionally.
|
|
eXraycer
Seriously Crusin Dubber

Posts: 166
Threads: 27
Registered: May 16th, 2012
Member Is Offline
Theme: UltimaBB Pro Blue ( Default )
|
posted on April 29th, 2013 at 03:55 PM |
|
|
Yes I heard about the CV's requiring a little massage (dimple) to the frame fork where they touch.
|
|
vlad01
Compulsive Aussie Vee Dubber
     
Posts: 4270
Threads: 109
Registered: June 3rd, 2010
Member Is Offline
Location: Kyneton, VIC
Theme: UltimaBB Pro Blue ( Default )
Mood: Side ways
|
posted on April 29th, 2013 at 08:17 PM |
|
|
yeah if you use the suby box it can clear it, stock probably not and need to be clearanced.
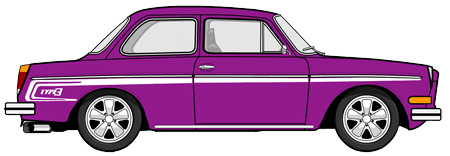
71 notchback,
Past owner of, 70 NB, 73 SB and 72 FB TLE
|
|
eXraycer
Seriously Crusin Dubber

Posts: 166
Threads: 27
Registered: May 16th, 2012
Member Is Offline
Theme: UltimaBB Pro Blue ( Default )
|
posted on May 4th, 2013 at 11:37 PM |
|
|
Thought I'd never have to do this but I dug out the old motor and bolted it up to the transmission. I needed to see if the heater boxes where going
to interfere with my Kafer bar setup so it was important to have them in plain sight before I tacked anything together. The old measure twice, cut
once theory.
So I started with this. My converted swing axle rear suspension with IRS pivot boxes in position ready for welding.

Cleaned and ready.

Cut crossbar. Used 1.5" chromoly tube for crossbar and 1" for the diagonals. Crossbar and forward diagonals will be solid welded. Rear diagonals
clearly need to be removable in order to be able to remove the transmission so I decided to use clevis joints for a double shear connection to the
through-bolt.

I notched the crossbar to sit on top of the shocktower shoulder.

Welded clevis joint tabs onto the HD rear trans mount.

Same for the top on the crossbar. Note, I found using hose clamps holds the Clevis joints on the tube until I weld them. Decided that I'm not gonna
make any of the diagonals adjustable. I see lots of Kafer bar kits with adjustable ends but I figure that's only necessary from a universal
off-the-shelf product perspective. Since I'm making my bars specifically to suit my car then there's no need to have them adjustable.

Its really tight trying to make it work with the heater boxes and heater cable lever. This is the only way to do it if you have any intention of
keeping the heaters.

Tacked rear diagonals in position.

Made front diagonals but they will not be tack welded. Will give us more room to get the IRS pivot boxes welded first.

|
|
eXraycer
Seriously Crusin Dubber

Posts: 166
Threads: 27
Registered: May 16th, 2012
Member Is Offline
Theme: UltimaBB Pro Blue ( Default )
|
posted on May 8th, 2013 at 12:28 PM |
|
|
Major milestone hit. Dropped the subframe to the fabricators for tig welding. Using a shop in Seven Hills called Racers Choice. Recommended by Rod
Andrews Race car supplies who supplied the moly tube for the kafer bars. Was going to use Rod for the welding but he's too busy at the moment.
A final thing before dropping it off: The area on the top frame horn metal near the pivot bolt exposes the pivot bolt a little and needs to be raised
so that you don't inadvertently weld the pivot bolt in the process. A little massage with some pliers and a hammer. Note the top of the frame horn is
thinner metal to the bottom half of the frame horn. I'm guessing that's because the top is in tension with the weight of the motor so it doesn't
need to be as heavy gauge. This is not the best when it come to attaching the Kafer bar forward struts to the top of the frame horn near the pivot
bolt. The Racers Edge fabricator recommended plating it with 3mm thick plate to spread the force then weld the diagonal brace to it. I was very happy
he mentioned that. I was gonna ask his opinion on the strength of that connection and if he though it needed reinforcing but he beat me to it. Gave me
more confidence in their work. I'm by no means building this to be a racecar but I think it's important to build it to last. I don't want to pull
it all out in six months to fix cracked welds.
This is the area I'm talking about.

You know if you want to do this sort of conversion you should consider doing the notching-in work yourself if you have the patience. It will save a
lot of money because most shops will charge it on hourly rate or if they quote a lump sum figure then it will either be expensive or worse still, too
cheap and then they will rush it to save their arse. You just can't rush this sort of work. It's the worst part of the entire job and consumes hours
of tedious work but you'll know it's done right and if you're careful and don't get over-zealous cutting the hole you can present the job to a
welder with very small gaps (1-2mm) suitable for intricate welding without too much filling. When they have to fill gaps with weld it imparts a lot of
heat into the surrounding area and could lead to brittle metal and cracking. Near-enough is not good enough unfortunately. I got the OK from the
welder for my prep work so I'm happy!
|
|
satori
Wolfsburg Wizard
 
Posts: 497
Threads: 243
Registered: May 9th, 2008
Member Is Offline
Location: Adelaide
Theme: UltimaBB Pro Grey
|
posted on May 8th, 2013 at 06:16 PM |
|
|
Wow dude. Thats some really great work. What engine are you going for.
[URL=http://s1226
|
|
eXraycer
Seriously Crusin Dubber

Posts: 166
Threads: 27
Registered: May 16th, 2012
Member Is Offline
Theme: UltimaBB Pro Blue ( Default )
|
posted on May 8th, 2013 at 10:03 PM |
|
|
Yeah it's a solid motor that i picked up as an unassembled box of new and reco parts based on a reconditioned AS 21 block that will be set up as a
1916cc.
Mahle pistons a barrels 94mm I think. I know the head is reconditioned but not standard with double valve springs, larger valves, higher ratio rocker
arms, electronic ignition instead of contact points, crank is stock length welded and balanced. Some of the exact specs I will get once my engine
builder puts it together. Bought for less than the sum of its parts so I had to roll with what I got. Figured that since it was the cc config I
wanted with high quality core components that it was a solid start. My engine builder is a formula vee racer who is a personal friend. He's builds
very competive f'vee engines for himself for 30 years and is enjoying this build cause its a refreshing change to build an engine unrestrained by
class specs.
Some extras I'm doing are a mini 60 amp alternator conversion, 40idf webers (reconditioned Italian made), engle 120 cam, straight cut forged timing
gears, external oil cooler, shallow depth sump extension. The list is growing. Should be a solid unit.
|
|
vlad01
Compulsive Aussie Vee Dubber
     
Posts: 4270
Threads: 109
Registered: June 3rd, 2010
Member Is Offline
Location: Kyneton, VIC
Theme: UltimaBB Pro Blue ( Default )
Mood: Side ways
|
posted on May 9th, 2013 at 10:01 AM |
|
|
Is there welders like this in Melbourne?
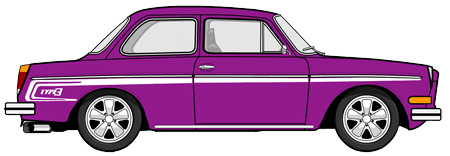
71 notchback,
Past owner of, 70 NB, 73 SB and 72 FB TLE
|
|
eXraycer
Seriously Crusin Dubber

Posts: 166
Threads: 27
Registered: May 16th, 2012
Member Is Offline
Theme: UltimaBB Pro Blue ( Default )
|
posted on May 9th, 2013 at 11:53 AM |
|
|
Skinned Knuckles in Melbourne might help. Check out his website. He does a lot more than narrowed bus beams.
I'm sure anyone who builds racecar roll cages can do this work too.
|
|
Pages: 1 2 3 |