[ Total Views: 242069 | Total Replies: 60 | Thread Id: 9938 ] |
Pages: 1 2 3 |
|
tassupervee
A.k.a.: Knob Jockey
Custom Title Time!
That really hurts doesnt it!
   
Posts: 1171
Threads: 25
Registered: September 21st, 2003
Member Is Offline
Location: Huon Valley SouthernTasmania
Theme: UltimaBB Psyche Blue
Mood: Moody!
|
posted on November 4th, 2003 at 09:59 PM |
|
|
Sorry in advance guys for the long post but there are a few issues here to cover.
Wes
You are running a good system by feeding the surge tank via an aux. LP pump. Running the return from the HP pump back to the surge tank is almost
unnecessary tho.
Nothing wrong with this system however. Blends warmed fuel from the engine with cooler fuel from the main tank and ensures the EFI pump is always
provided with a head of fuel.
Surge tanks are necessary when there is no swirl pot in the main tank or mainly in the case of circuit racing cars that, due to high cornering
"G" forces, will see the fuel surging up the sides of the tank and well and truly uncovering the fuel outlet as the tank level drops around
sweeping bends. It would be adviseable in an offroad machine as well as these things wil often experience high angles for extended time and may not
necessarily full of fuel at the time.
This type of return from the engine and the LP feed point of the surge tank should be well above the HP pump inlet or outlet depending on the setup,
to prevent any heated fuel directly returning back into the HP pump and any air that may be introduced into the system from surging in the main tank
from making its way into the HP pump. This is bad
It is acceptable to feed the surge tank/EFI pump by gravity and a 12mm line is adequate provided the run is short and directly down. Bigger is best
here.
EFI pumps, by their nature, take a very dim view to "sucking" and this can easily result in cavitation, noisy running of the pump, which
leads to overheating and very premature failure. They should always be sited below the main tank to ensure a "head" of fuel at all times.
Ignoring the surging around corners issue of some aftermarket EFI setups, with no surge tank or swirl pot in the main tank and the resulting
cavitation, will lead to premature wear of the pump and possible failure of the pump.
This is the reason for having a "swirl pot" in the main tank, in the case of pretty much every EFI car ever made or a remote surge tank,
either gravity fed, if it is possible to get the surge tank directly under the main tank, with a vent line from the very top of the surge tank
breathing back into the top of the main tank or, (often in most cases), if not, then a aux. LP pump feeding the surge tank (which can then be located
anywhere)
The return of the surge tank can be teed into the return line from the engine and this is usual practise. This return line "should"
discharge right down in the bottom of the main tank. The return from the engine should never be plumbed directly back into the inlet side of the EFI
pump as the fuel will slowly increase in temp leading to the problems with fuel pressure that Wes has described.
There are plenty of dodgey setups with the return fuel splashing into the main tank from the top of the tank that still work just fine.
The issue if vapour and heat expansion/breathing of the main tank is usually dealt with via a regulated/ restricted vacuum source to the tank.
This is why you are often greeted with a loud hissing sigh when you open the tanks at the fuel stop. It is air breathing IN.
Anothe simple strategy to deal with tank breathing is to plumb the main tank vent line into the inlet somwhere between the air filter and the throttle
body.
The issue of say, a Facet type of solid state LP pump (which I think Wes is running there) not having the flow capacity of the HP EFI pump is not
correct.
Those small solid state pumps are flow rated wayyy above any EFI pump flow demands.
I use a small 40 dollar solid state pump designed for atmo 6 cylinder carby cars as an aux lift pump in my Nissan FJ20det powered Econovan. This
engine is turbocharged and dyno's at around 150 KW on stock boost setting.
I dont even use a swirl pot or surge tank and the little lift pump simply blows directly up the bum of the EFI pump as there is no bottom feed in the
tank for the pump. This would mean the EFI pump must "pull" the fuel out of the tank which is no good and results in EFI pump damage and
eventual failure.
You will find that the EFI pumps are rated with no restriction and as the EFI fuel pressure pressure required rises, say typically around 45 psi or so
and well above such as in a rising rate EFI system, the output flow rate reduces proportionately.
The issue of feeding 7 psi up the bum of the EFI pump via an aux. pump in series, and resulting in upping the eventual pressure fuel output pressure
of the EFI pump is only correct in the case of an unregulated non-returning or static system. pretty much like a standard carby setup
In all EFI setups, all the fuel pressure regulation is done after the fuel injector rail, on the return line to the tank. So the pressure differences
will just normalise between and after the two pumps as they share the load,
The regulator will simply bleed off excess pressure by providing a relatively unrestricted return path of fuel that exceed the flow rates the pumps
can supply so the flow rate increases and the pressure simply drops untill the regulator reaches its preset output pressure. This type of regulation
results in a constant flow of fuel thru the pump that lubricates and importantly, cools the pump. Also, EFI pumps are unregulated, positive
displacement pumps and if the output of the pump is blocked off, as in a non-returning or static system, the pump will pretty much stall and burn out
in short time.
It is often practice to use 2 EFI HP pumps in series, one near the tank and another somewhere along the line or in the engine bay being a "helper
pump" that will act as a flow/pressure backup especially in say, a rising rate turbo EFI system where the flow demands with a rising rate
regulator will exceed the output of a single pump resulting in fuel pressure drop.
VL turbo Crappadores are an example of a dual inline EFI pump setup.
Wes's system is pretty much the last word in a bulletproof fuel system but worrying about the heat buildup in the main tank and the resultant
extra plumbing is pretty much unnecessary.
The heat buildup in the main tank is not that great bearing in mind the radiating surface area of a typical fuel tank so the idea of adding a fuel
cooler to the setup is totally unnessary.
The third setup detailed by Wes is more than adequate to handle anything you can throw at it and my preferrence would be, in the interests of
simplicity, would be to Tee the surge tank return into the EFI return.
Wes has fabricated a square tank but a far simpler to make solution is to use a length of 3" or so exhaust pipe and simply weld on a square plate
on the bottom and if, as in Wes's case, using an in-tank submerged type of pump, you will need to make the top plate of the tank removable so the
pump can be attached to the plate and wires and outlet pipe and such can run thru it.
There is alway the issue with this arrangement of successfullky sealing the wiring coming thru the lid but this can be helped out by lowering the
breather return line from the surge tank well below the very top of the surge tank. You then only have to deal with splashing of the fuel rather than
a head of fuel trying to weep out past the wires/seals.
This is probably an unnecessarily complicated way to do things and sealing up the surge tank and using a simple external, inline, hosetail type of EFI
pump plumbed directly off the bottom of the surge tank is by far the easiest way to go.
I suspect that Wes happend to have the in-tank submerged type EFI pump floating around on hand and has the patience and facilities at hand to sit down
and bother to fabricate and successfully seal a removeable lid to his tank.
By simply brazing 2 square flat 2mm plates to the top and bottom of the 3" tube is shit easy and then it is a doddle to braze on the various
inlet and outlet hosetails needed. These square plates can be extended and bent at right angles to make simple mounting brackets if need be.
Sealed surge tanks are available commercially in various capacities starting around 120 bucks in mild steel and a fair bit more for ally iffen you
wish to polish it up for wank value.
They take about an hour to make and cost a few dollars for some steel hosetails, the zorst tube and end plates
Too easy.
Have fun dudes
L8tr
E
Im not a complete idiot, quite a few parts are missing....
|
|
Baja Wes
Bishop of Volkswagenism
V6 Baja Pioneer
    
Posts: 3119
Threads: 94
Registered: August 26th, 2002
Member Is Offline
Location: Brisbane
Theme: UltimaBB Pro Blue ( Default )
Mood: Content
|
posted on November 5th, 2003 at 08:33 AM |
|
|
All good comments. There's obviously more than one way to skin a cat.
The only point I disagree with is this one...
Quote: | Originally
posted by tassupervee
The issue of say, a Facet type of solid state LP pump (which I think Wes is running there) not having the flow capacity of the HP EFI pump is not
correct.
Those small solid state pumps are flow rated wayyy above any EFI pump flow demands.
|
My facet fuel pump is rated at 2.2 L/min flow. Check their website it agrees with that figure (132L/hr).
My HP pump is rated at 3-4 L/min. So getting towards twice the flow rating.
It is simply because the LP pumps are designed to feed as much fuel as is needed for the engine to burn, whereas HP pumps are designed to pump much
more than that to continuously flush the fuel rail with cooler fuel.
And to explain my surge tank a little more :thumb ;
I used an intank pump from the same car as my V6 came from. That way I knew it was the right size. This set-up is compact and ensures mud cannot get
into the HP pump. The intank HP pump also has a nice filter bag on the bottom. The arrangement is why my surge tank is square.
As for having to seal wiring through the lid, that is not an issue. The intank pump has a mounting flange which the fuel pipes and wires are already
sealed through. All I needed was a surge tank with the same mounting flange as the stock V6 tank. I got a friend to make the surge tank to suit, and
it cost me a carton or $40 or something 
|
|
PurpleT3
Fahrvergnugen
  
Posts: 880
Threads: 55
Registered: April 8th, 2003
Member Is Offline
Location: Knox, Melbourne
Theme: UltimaBB Pro Blue ( Default )
Mood: knackered
|
posted on November 5th, 2003 at 10:04 AM |
|
|
Standard VW EFI
Sorry to intrude on your discussion re aftermarket EFI.
I'm in the process of reassembling my bog stock FI type 3. I haven't noticed any swirl pots or surge tanks, there's nothing in the
tank. Are they hidden somewhere? Have I just missed them, or do they not exist? If so does this mean I'll get fuel starvation when cornering
hard? Maybe a standard type 3 cann't corner hard enough to suffer this problem.
Ain't nothin' like the wind in your hair.
|
|
Baja Wes
Bishop of Volkswagenism
V6 Baja Pioneer
    
Posts: 3119
Threads: 94
Registered: August 26th, 2002
Member Is Offline
Location: Brisbane
Theme: UltimaBB Pro Blue ( Default )
Mood: Content
|
posted on November 5th, 2003 at 01:16 PM |
|
|
I know nothing about EFI type 3's, so can't help 
You'd only notice when cornering hard and low on fuel.
|
|
kombi_kid
Super Moderator
Good Kid too many projects
     
Posts: 124
Threads: 341
Registered: August 27th, 2002
Member Is Offline
Location: brisvegas
Theme: UltimaBB Pro Blue ( Default )
|
posted on November 5th, 2003 at 03:11 PM |
|
|
hey
all good info here!!! its hard for me to understand it all but its still a good read!!!
cheers
rhys
it aint just cool its aircool'd
|
|
tassupervee
A.k.a.: Knob Jockey
Custom Title Time!
That really hurts doesnt it!
   
Posts: 1171
Threads: 25
Registered: September 21st, 2003
Member Is Offline
Location: Huon Valley SouthernTasmania
Theme: UltimaBB Psyche Blue
Mood: Moody!
|
posted on November 5th, 2003 at 09:28 PM |
|
|
Wes
That is correct to a certain extent but the flow rates specified for most EFI pumps are a theoretical flow rate based on ambient with no
restriction.
As you raise the delivery pressure above ambient the flow rate of the EFI pump drops off progressively untill there is a point where the pump will not
supply any fuel at all but at its maximum pressure.
This can be easily demonstrated by simply blocking off the outlet of the pump and the pressure should rise thru the roof. In fact, as EFI pumps are a
positive displacement type of pump, the pump will simply stall and burn out but for the purposes of the exercise, we will presume the pump is
deliovering its highest output pressure with the pump close to stalling. The pump will deliver X PSI. possibly even hundreds of PSI dependant on the
power of the electric motor.
Progressively open the fuel outlet and the pump will deliver more and more fuel flow and proportionately less and less delivery pressure.
This is the relationship that must be addressed when choosing a pump to suit a particular horsepower rating of the engine setup.
Those solid state pumps will happily out perform the EFI pump in flowrates when the EFI pump is actually running at system pressure.
This is why I, and a million other aftermarket EFI users, have absolutely zero qualms in running a cheap solid state lift pump feeding the surge tank
or as in my case, directly up the bum of the EFI HP pump.
Try removing the tank return line with the pump powered and the engine off and measure the time it takes to bypass a liter.
The do the same with the surge tank LP lift pump.
No brainer. You'll see what I mean.
As far as the construction of your surge tank, that is what I had figured.
I suspected you had the original pump already. It was certainly handy having the removeable top of the original tank as i reckon it would have taken
quite some time to fabricate one from scratch.
hence my dissertation on constructing one from scratch.
l8tr E
Im not a complete idiot, quite a few parts are missing....
|
|
Herbie
Insano Dub Head
53 Bugs are not nearly enough
  
Posts: 764
Threads: 51
Registered: September 3rd, 2002
Member Is Offline
Location: GoldCoast
Theme: UltimaBB Pro Blue ( Default )
Mood: Nihil curo de ista tua stulta superstitione.Utinam logica falsa tuam philos
|
posted on November 6th, 2003 at 05:27 AM |
|
|
I thought we buried this thread months ago.
Why the sudden awakening?
62 Ragtop Herbie with a little extra oomph.
|
|
Baja Wes
Bishop of Volkswagenism
V6 Baja Pioneer
    
Posts: 3119
Threads: 94
Registered: August 26th, 2002
Member Is Offline
Location: Brisbane
Theme: UltimaBB Pro Blue ( Default )
Mood: Content
|
posted on November 6th, 2003 at 08:32 AM |
|
|
Quote: | Originally
posted by tassupervee
Try removing the tank return line with the pump powered and the engine off and measure the time it takes to bypass a liter.
The do the same with the surge tank LP lift pump.
|
I have tried that. I put a restriction in the outlet of my LP facet pump to quieten it down, which it did. Put that reduced the flow a little. I found
a happy medium where I was getting a little under 2L/min of fuel flow. I timed how long it took to fill a 2L ice cream bucket.
I did a similar thing with my front cut and HP pump when I was playing with it, and I tell you the HP EFI pump flows alot more out the return line (so
pumping at rated pressure) than my LP pump. For my pump combo it is a fact the HP pump is out flowing the LP pump. Maybe your combo is different.
I'll also point out the LP facet pumps pulse, whereas the HP pumps don't, so I wouldn't feed one into the other for that reason.
And a bit of tirvia, not all HP pumps are positive displacement. I have seen the sliding vane / roller cell and similar style positive displacement
pumps, but I have also seen centrifugal/axial turbine style HP pumps.
Oh, and I didn't have the flange from the EFI tank, I just got a flange made to suit my EFI pump, which has the pump side flange. My surge tank
was completely fabricated from stainless steel. If I was to do it again I would use aluminium as it would disperse the heat in the surge tank faster.
Herbie, if useful bits of info keep getting added, then the replies will keep coming. We learn from our mistakes, and other peoples mistakes too.
:thumb
|
|
tassupervee
A.k.a.: Knob Jockey
Custom Title Time!
That really hurts doesnt it!
   
Posts: 1171
Threads: 25
Registered: September 21st, 2003
Member Is Offline
Location: Huon Valley SouthernTasmania
Theme: UltimaBB Psyche Blue
Mood: Moody!
|
posted on November 6th, 2003 at 11:34 AM |
|
|
Hmmm I gotta check out the type of HP pum U R using as I have never seen a lift pump other than any of those generic pulse style things feeding the
surge tank.
Never!
On my FJ20det powered van and also on my wifes Pulsar Turbo ET the fuel flow on the return line AFTER the regulator is not nearly that high.
Pulsing into the HP pump is no issue. regulator deals with tha further down the line. Works perfectly
L8tr
E
Im not a complete idiot, quite a few parts are missing....
|
|
Baja Wes
Bishop of Volkswagenism
V6 Baja Pioneer
    
Posts: 3119
Threads: 94
Registered: August 26th, 2002
Member Is Offline
Location: Brisbane
Theme: UltimaBB Pro Blue ( Default )
Mood: Content
|
posted on November 6th, 2003 at 12:12 PM |
|
|
a few figures for the interested, fuel flow from EFI pumps, all at 40psi.
XE falcon = 1.8 L/min
VL holden = 2.3 L/min
6.9 Merc = 2.7 L/min
R32 GTR skyline = 4.5L/min
So finding a factory EFI pump that can out do the facet pump at typical fuel rail pressures isn't too hard.
Most people won't use a facet as a feed pump, and instead opted for the more expensive Carter lift pump. Since my car was taking about 45min for
the fuel to get too hot, I figured I only required a low performance facet pump to do the job.
But again there's a million ways to do it, and whatever works is fine.
|
|
tassupervee
A.k.a.: Knob Jockey
Custom Title Time!
That really hurts doesnt it!
   
Posts: 1171
Threads: 25
Registered: September 21st, 2003
Member Is Offline
Location: Huon Valley SouthernTasmania
Theme: UltimaBB Psyche Blue
Mood: Moody!
|
posted on November 6th, 2003 at 02:52 PM |
|
|
Yes indeed!
L8tr
E
Im not a complete idiot, quite a few parts are missing....
|
|
pete wood
A.k.a.: figure itout
23 Windows of Awesome
      
Posts: 6828
Threads: 389
Registered: January 15th, 2004
Member Is Offline
Location: Nth Nth StMarys, Sydney
Theme: UltimaBB Pro White
Mood: upgrades = jackstands
|
posted on August 30th, 2004 at 10:43 PM |
|
|
If anyone is interested, I run the same type of system in my car (EJ25 buggy) as wes does and it works absolutely fine. The only difference in mine is
that the surge tank is at the back of the car, not under the front main tank.
|
|
spectreeng
Learner Dubber
Posts: 1
Threads: 0
Registered: May 19th, 2006
Member Is Offline
Theme: UltimaBB Pro Blue ( Default )
|
posted on May 19th, 2006 at 08:40 AM |
|
|
Has anyone tried putting a pressure regulator right after the hp pump, with the hp pump underneath the car so that the "return" fuel doesn't get
heated up? I'm thinking with this method you could tee it back into the hp pump feed line since you're not introducing heat into the fuel. |
|
Baja Wes
Bishop of Volkswagenism
V6 Baja Pioneer
    
Posts: 3119
Threads: 94
Registered: August 26th, 2002
Member Is Offline
Location: Brisbane
Theme: UltimaBB Pro Blue ( Default )
Mood: Content
|
posted on May 30th, 2006 at 04:26 PM |
|
|
Quote: | Originally
posted by spectreeng
Has anyone tried putting a pressure regulator right after the hp pump, with the hp pump underneath the car so that the "return" fuel doesn't get
heated up? I'm thinking with this method you could tee it back into the hp pump feed line since you're not introducing heat into the fuel.
|
The way normal EFI regulators are set-up is before the regulator is the regulated pressure, and after it is no pressure (only what is required to
return the fuel). So if you put the regulator before the injectors then you don't have any pressure at the injectors.
|
|
GeorgeL
Officially Full-On Dubber
 
Posts: 231
Threads: 11
Registered: February 5th, 2006
Member Is Offline
Location: 7200 miles off the Queensland coast
Theme: UltimaBB Pro Blue ( Default )
|
posted on July 6th, 2006 at 07:07 AM |
|
|
One thing that I didn't see addressed in this very informative thread is the question of why the fuel heats up.
While the fuel may pick up some external heat in the fuel rail, most of the heating is done by the pressure regulator. The fuel pump pushes the fuel
along, putting energy into the fuel that it takes from the electrical system. When the fuel pressure is dropped by fluid friction in the pressure
regulator the energy that went to pressurizing the fuel becomes heat, increasing the temperature of the fuel. If the fuel is recirculated directly to
the inlet side of the pump it will get hot fast as it goes through the regulator again and again.
This is particularly bad when the engine is _not_ making power, as the fuel pump is constant flow and most of the fuel goes through the regulator at
low power settings. At higher power settings, considerable fuel flows through the injectors and is replaced by cold fuel from the tank.
The upshot of this is that recirculating a small volume of fuel at low power settings can result in rapidly heating the fuel past the vaporization
point. You can fix this by running the fuel through a finned cooler or simply by returning the fuel to the main tank, where the large skin area of
the tank will cool the fuel sufficiently.
|
|
Baja Wes
Bishop of Volkswagenism
V6 Baja Pioneer
    
Posts: 3119
Threads: 94
Registered: August 26th, 2002
Member Is Offline
Location: Brisbane
Theme: UltimaBB Pro Blue ( Default )
Mood: Content
|
posted on July 6th, 2006 at 11:52 AM |
|
|
Quote: | Originally
posted by GeorgeL
While the fuel may pick up some external heat in the fuel rail, most of the heating is done by the pressure regulator. The fuel pump pushes the fuel
along, putting energy into the fuel that it takes from the electrical system. When the fuel pressure is dropped by fluid friction in the pressure
regulator the energy that went to pressurizing the fuel becomes heat, increasing the temperature of the fuel. If the fuel is recirculated directly to
the inlet side of the pump it will get hot fast as it goes through the regulator again and again.
|
Hi George,
My first thought is, that ridiculous. But then I figured I better back it up with some math. 
Assume a HP pump is flowing 2.5L/min of fuel through the fuel rail, and is pressurising it to 45psi (the regulator set point). It can be easily
calculated that there is 12.9W of energy in this fuel, so dropping the pressure back to zero through the regulator could only possibly generate 12.9W
of heat energy. In reality less than that would be converted to heat.
So how much heating will 12.9W of heat do? Not much. When your driving you'd be using about 6L/hr of fuel. If your surge tank was completely
insulated then your 12.9W of heat would try to warm the 6L (and would only have 1 hour to do it before it was replaced by another 6L of fuel). Knowing
the specific heat of petrol you can calculate that you'd only heat the fuel by 4 degrees in that hour (assuming perfect insulation). That isn't
enough to be a problem.
Then if the surge tank wasn't perfectly insulated you could calculate how much it cools. For a 100x100x200 tank you can calculate the expected
cooling due to natural convection, and what the equilibrium fuel temperature would be (with 6L/hr passing and 12.9W heating). I get the expected fuel
temperature rise to be only 2.7 degrees C.
So basically the heat generated by the regulator is virtually nothing and has a very very little effect.
My fuel rail is cast aluminium, and bolts to the manifold. So there is heaps of heat conduction from the head to the manifold to the fuel rail and
into the fuel.
|
|
pete wood
A.k.a.: figure itout
23 Windows of Awesome
      
Posts: 6828
Threads: 389
Registered: January 15th, 2004
Member Is Offline
Location: Nth Nth StMarys, Sydney
Theme: UltimaBB Pro White
Mood: upgrades = jackstands
|
posted on July 6th, 2006 at 05:58 PM |
|
|
So Wes, does the fuel heat up much off the inlet manifold in your car?
I know you were haivng some dramas with something like a vapour lock a while back. Did you findout what it was and why?
|
|
Baja Wes
Bishop of Volkswagenism
V6 Baja Pioneer
    
Posts: 3119
Threads: 94
Registered: August 26th, 2002
Member Is Offline
Location: Brisbane
Theme: UltimaBB Pro Blue ( Default )
Mood: Content
|
posted on July 7th, 2006 at 08:51 AM |
|
|
the vapour lock thing is described earlier in this thread. It was when I had the fuel rail return line going into the surge tank. So the heat from the
intake would heat the fuel as it went through the rail. After 40min the fuel in the surge tank would be hot enough to cause problems and make the car
stop momentarily.
Now I have a LP pump circulating fuel between the surge and main tank I don't have any problems. It keeps the temp even between the two tanks, and
the surface area of the main tank is enough to keep it cool.
|
|
GeorgeL
Officially Full-On Dubber
 
Posts: 231
Threads: 11
Registered: February 5th, 2006
Member Is Offline
Location: 7200 miles off the Queensland coast
Theme: UltimaBB Pro Blue ( Default )
|
posted on July 8th, 2006 at 10:21 AM |
|
|
Quote: | Originally
posted by Baja Wes
Quote: | Originally
posted by GeorgeL
While the fuel may pick up some external heat in the fuel rail, most of the heating is done by the pressure regulator. The fuel pump pushes the fuel
along, putting energy into the fuel that it takes from the electrical system. When the fuel pressure is dropped by fluid friction in the pressure
regulator the energy that went to pressurizing the fuel becomes heat, increasing the temperature of the fuel. If the fuel is recirculated directly to
the inlet side of the pump it will get hot fast as it goes through the regulator again and again.
|
Hi George,
My first thought is, that ridiculous. But then I figured I better back it up with some math. 
Assume a HP pump is flowing 2.5L/min of fuel through the fuel rail, and is pressurising it to 45psi (the regulator set point). It can be easily
calculated that there is 12.9W of energy in this fuel, so dropping the pressure back to zero through the regulator could only possibly generate 12.9W
of heat energy. In reality less than that would be converted to heat.
So how much heating will 12.9W of heat do? Not much. When your driving you'd be using about 6L/hr of fuel. If your surge tank was completely
insulated then your 12.9W of heat would try to warm the 6L (and would only have 1 hour to do it before it was replaced by another 6L of fuel). Knowing
the specific heat of petrol you can calculate that you'd only heat the fuel by 4 degrees in that hour (assuming perfect insulation). That isn't
enough to be a problem.
Then if the surge tank wasn't perfectly insulated you could calculate how much it cools. For a 100x100x200 tank you can calculate the expected
cooling due to natural convection, and what the equilibrium fuel temperature would be (with 6L/hr passing and 12.9W heating). I get the expected fuel
temperature rise to be only 2.7 degrees C.
So basically the heat generated by the regulator is virtually nothing and has a very very little effect.
My fuel rail is cast aluminium, and bolts to the manifold. So there is heaps of heat conduction from the head to the manifold to the fuel rail and
into the fuel.
|
You calculations are correct, but you're assuming perfect efficiency from the fuel pump, which doesn't seem to be the case. I looked up the typical
current draw of a fuel pump and it is in the range of 5-8 amps. At 14V, this would be a power input of 70-112W.
Now, let's consider surge tank and plumbing of volume 1 liter. one liter of fuel would have mass 0.73kg. The specific heat of gasoline is about
2020J/kg C
That means that, if we consider the 100W or so of power going into the pump to be all going into heating the fuel, the liter of fuel will warm by
about .067C every second, or about 4 degrees per minute. Gasoline has a wide range of boiling points. but if we assume a fuel temperature in the tank
of 20C and a boiling temperature of 60C we have about 10 minutes before the fuel in the surge tank loop will reach 60C simply from the power input of
the pump.
Now, there are a lot of assumptions here.
I've neglected heat loss from the system by convection. I don't think that this would be all that much as the fuel circuit tends to be cooler than
the ambient temperatures near the engine.
I've also neglected the replacement of fuel in the loop as it is burned. If the system burned a liter of fuel every 10 minutes while idling it would
keep the fuel at about 40C and therefore a bit below boiling, but that would be a fairly high idle consumption!
Add to this the heat input from your fuel rail on the manifold and it is pretty easy to see how the fuel can get too hot pretty fast.
This is why I feel that the regulator and pump do make a significant contribution to fuel heating, particularly at low power settings.
George
|
|
Baja Wes
Bishop of Volkswagenism
V6 Baja Pioneer
    
Posts: 3119
Threads: 94
Registered: August 26th, 2002
Member Is Offline
Location: Brisbane
Theme: UltimaBB Pro Blue ( Default )
Mood: Content
|
posted on July 8th, 2006 at 11:30 PM |
|
|
George,
In your first post I thought you just meant the regulator causes a lot of heating. Now I see you mean heat from the pump itself. Yes these pumps are
very inefficient, so you put quite a lot of electrical energy into them and get a relatively small amount of pressure and flow energy out. That's why
I was saying the heat from the pressure change across the regulator is small.
My pump doesn't run the high amps you've quoted. That seems like the peak amps with a blocked outlet. I think a typical HP pump is closer to 3-5amp.
I run a HP and LP pump off the same 10amp fuse with no issues, so I doubt the HP pump is over 5 amps.
The calc should be done with the car driving, as not many people leave their engines idling for more than 10 minutes.
Also most people with small seperate surge tanks use external pumps, so the heat from the inefficiency of the electric motor and mechanicals of the
pump do get dissipated as convective heat more so than my situation where I have an intank pump in the surge tank.
We should be quiet now before someone large and hairy gives us a wedgy
|
|
choppa
Seriously Crusin Dubber

Posts: 190
Threads: 42
Registered: October 14th, 2002
Member Is Offline
Location: Perth
Theme: UltimaBB Pro Blue ( Default )
Mood: Itchy
|
posted on October 6th, 2006 at 02:05 AM |
|
|
Just my 2cents worth Wes.
Initially you said the fuel in your swirl pot was boiling.
Could this be cos the pot wasnt vented properly , I have heard that liquid and specially fuel will boil at room temperature if in a vacume.
I say this cos I remember when I first built my fuel system , similar to yours with no lift pump my pot boiled too.
To fix this I enlarged the gravity feed from the tank to the pot to 5/8 I think or maybe 1/2 inch. I also put a 3/8 breather line all the way up to
the highest point in the boot(from the pot) and connected it to the fuel filler pipe and then down to the front of the car near the axle as a open
vent to atmosphere. This sorted out the boiling. But the fuel still gets hot and my lines are external, under the sill.
These days the only time i get any stalling or stumbling is in 3rd at full noise at the strip, if the fuel level is below 1/4 full. Thats wierd cos my
pot would be close to 2 litres capacity and made of 5 inch exhaust tube.
So my question is. In this thread I have seen no mention of vents. I would be interested to see any tried and tested vent systems.
Mark
|
|
Baja Wes
Bishop of Volkswagenism
V6 Baja Pioneer
    
Posts: 3119
Threads: 94
Registered: August 26th, 2002
Member Is Offline
Location: Brisbane
Theme: UltimaBB Pro Blue ( Default )
Mood: Content
|
posted on October 6th, 2006 at 12:28 PM |
|
|
first, regarding boiling fuel. Any liquid boils when it reaches the vapour pressure, and the vapour pressure varies with temperature.
We are all familiar with water. At 25 degrees it's vapour pressure is 3.2kPa(a). [where (a) is absolute pressure] Atmospheric pressure is
101.3kPa(a). So you would need a vacuum pressure of 98.1kPa(g) (guage pressure) to boil water at 25 degrees.
The vapour pressure of water at 100 degrees is equal to atmospheric pressure, therefore that is it's boiling point.
Petrol is much different. It's vapour pressure is much closer to atmospheric, and it's boiling point is much lower. It's hard to find exact numbers
for those. But anyway...
I ran a pair of 10mm lines into my surge tank, but as there was no real flow the temp in the surge tank still climbed.
Putting a vent on the surge tank would be a bad idea. As you start getting hot vapourised fuel returning to your surge tank, it raises to the top, and
out your vent. The advantage is as fuel goes out the vent, new fuel will come in your other lines and prolong the length of time until you get a
cavitating pump / vapour lock type problem.
The disadvantage is that fuel going up the vent line probably keeps going along the vent line and out to atmosphere. It probably isn't doing your
fuel economy any good.
It is also bad for the environment, and probably illegal. Cars from somewhere around the mid 70's were fitted with carbon cannisters to catch the
fuel that tries to escape out the vent line. If you fit a later model motor you also legally need to run the carbon cannister or whatever emmissions
gear the donor car was fitted with.
The carbon cannisters are designed to deal with a little amount of fuel. If you are boiling off the fuel in the surge tank at a quicker rate, you will
likely flood the carbon cannister, and eventually fuel will leak out the vent line. This is a fire hazard, and the carbon cannister a petrol bomb of
sorts.
Basically car manufacturers try to keep the hot fuel away from the vent, to prevent the evaporation / vapourisation fuel loss. This is why normal cars
have the fuel return line go to the bottom of the tank, near the swirl pot. By the time the hot fuel from the return line makes it's way through the
tank and near the fuel level surface, it should have cooled down.
|
|
Turbo54
Veteran Volks Folk
   
Posts: 2220
Threads: 268
Registered: July 13th, 2004
Member Is Offline
Theme: UltimaBB Pro Blue ( Default )
Mood: Boost'n
|
posted on November 14th, 2006 at 04:45 PM |
|
|
This is hurting my head.... anyone else feel like this.
I have just finished designing and laying some of this out in my car. I am trying to make it as simple as possible and was even thinking of not
running a looped system like my friends 1000hp LS1. I decieded to go looped in the end and the system goes like this. This is all -6 (10mm).
Tank – gravity feed through a strainer into top of small 750ml surge tank.
Surge tank gravity feed into bosch 910 pump.
Pump – filter
Filter – into fuel lines that run through tunnel to back of car.
This section hasn't been worked out yet as I have been waiting to get the injection manifolds back for fabricator.
SARD rising rate regulator – into return pipe back down tunnel and into surge tank.
I understand that anything compressed ie air from a turbo or fuel from a pump is going to get hot but from what I understand from here is that I am
going to be circulating really hot fuel. Also I was hoping that the air bubbles and vapours would rise back up into the main tank from the surge tank
be itself. Will this become a vapour lock. Should that peice of hose be -10 to allow for air and fuel.
It is very similar to Herbies drawing on the second post.
T54
C'mon kids gather round,
there's a new sensation hitting town,
It's moving straight, low to the ground,
it'll pick you up when your feeling down.
|
|
Baja Wes
Bishop of Volkswagenism
V6 Baja Pioneer
    
Posts: 3119
Threads: 94
Registered: August 26th, 2002
Member Is Offline
Location: Brisbane
Theme: UltimaBB Pro Blue ( Default )
Mood: Content
|
posted on November 15th, 2006 at 08:05 AM |
|
|
what you have described is very very similar to my first set-up, except I had an internal pump in the surge tank.
It looked like this;

It would be fine for about 40minutes of driving, and then the fuel in the surge tank would get too hot and the engine would cut out. I would expect
you would have the same problem.
|
|
T-34
A.k.a.: Mick
Officially Full-On Dubber
 
Posts: 234
Threads: 35
Registered: February 11th, 2004
Member Is Offline
Location: Adelaide
Theme: UltimaBB Pro Blue ( Default )
|
posted on April 15th, 2007 at 11:30 AM |
|
|
Just reading through this thread as I'm about to sort out the EFI on my car and something struck me about the heat problem you were experiencing in
the surge tank.
These are just my thoughts / opinions - so they could be wrong - but just a little food for thought...
Without a regulator the pump would flow the maximum rated flow (provided the fuel lines were the correct size and provided no restriction).
The regulator is added to regulate the pressure to the fuel rail such that it is a constant pressure. The regulator acts as a restrictor in the line -
restricting the flow and thus maintaining the pressure on its primary side.
The flow restriction places extra load on the pump which in turn generates extra heat within the pump itself.
Normally with a submersible pump the fuel in the tank acts to cool it, with the pump sitting in such a small tank this does not happen - it simply
heats the fuel and the tank up as there is not enough volume of liquid to dissipate the heat
This heated fuel in turn heats up the injector rails when it is circulated through the system.
Just my 02c
Mick.
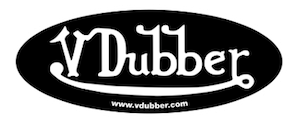
|
|
Baja Wes
Bishop of Volkswagenism
V6 Baja Pioneer
    
Posts: 3119
Threads: 94
Registered: August 26th, 2002
Member Is Offline
Location: Brisbane
Theme: UltimaBB Pro Blue ( Default )
Mood: Content
|
posted on May 15th, 2007 at 05:39 PM |
|
|
Quote: | Originally
posted by T-34
This heated fuel in turn heats up the injector rails when it is circulated through the system.
|
My intake (which the fuel rail is bolted to) is consistantly way hotter than my surge tank. So there is no way the fuel is heating up the injector
rail (as the fuel is cooler than the intake that the injector rail is bolted to).
My system has been working perfect for the last (almost) 4 years . I
would like to build a bigger capacity fuel tank with an in-built surge tank though. It would certainly clean up the front of the car. I am also a
little concerned that on big hits offroad the long tie-rod will flex enough to take out the surge tank (I have found evidence that it has flexed and
rubbed on the surge tanks fuel lines). Ah, there's always something to do to the car...
|
|
kombi_kid
Super Moderator
Good Kid too many projects
     
Posts: 124
Threads: 341
Registered: August 27th, 2002
Member Is Offline
Location: brisvegas
Theme: UltimaBB Pro Blue ( Default )
|
posted on November 22nd, 2007 at 03:15 PM |
|
|
so the low pressure pump just pumps the fuel between the the surge tank and the fuel tank and the high pressure pump pulls the fuel from the surge
tank into the fuel rail and back to the surge tank?
going to put a surge tank in my bus i think on hard cornering with no surge tank it suffers a little
cheers
rhys
it aint just cool its aircool'd
|
|
1303Steve
A.k.a.: Steve Carter
Scirocco Rare
       
Posts: 8650
Threads: 564
Registered: August 27th, 2002
Member Is Offline
Location: Sydney, NSW
Theme: UltimaBB Pro Blue ( Default )
Mood: Parrot Heading
|
posted on November 22nd, 2007 at 10:28 PM |
|
|
Hi Rhys
If a Kombi tank is the same as yours, try and get a factory EFI one.
Steve
|
|
kombi_kid
Super Moderator
Good Kid too many projects
     
Posts: 124
Threads: 341
Registered: August 27th, 2002
Member Is Offline
Location: brisvegas
Theme: UltimaBB Pro Blue ( Default )
|
posted on November 27th, 2007 at 09:12 AM |
|
|
i was thinking that they would be the go!
cheers
rhys
it aint just cool its aircool'd
|
|
leweydafly
Learner Dubber
Posts: 15
Threads: 2
Registered: September 10th, 2008
Member Is Offline
Location: Dandebong
Theme: UltimaBB Vintage
Mood: Somewhat indifferent
|
posted on September 15th, 2008 at 09:55 PM |
|
|
Quote: | Originally
posted by T-34
Just reading through this thread as I'm about to sort out the EFI on my car and something struck me about the heat problem you were experiencing in
the surge tank.
These are just my thoughts / opinions - so they could be wrong - but just a little food for thought...
Without a regulator the pump would flow the maximum rated flow (provided the fuel lines were the correct size and provided no restriction).
The regulator is added to regulate the pressure to the fuel rail such that it is a constant pressure. The regulator acts as a restrictor in the line -
restricting the flow and thus maintaining the pressure on its primary side.
The flow restriction places extra load on the pump which in turn generates extra heat within the pump itself.
Normally with a submersible pump the fuel in the tank acts to cool it, with the pump sitting in such a small tank this does not happen - it simply
heats the fuel and the tank up as there is not enough volume of liquid to dissipate the heat
This heated fuel in turn heats up the injector rails when it is circulated through the system.
Just my 02c
Mick.
|
i think you hit the nail on the head there. better cooling having the pump submersed in the main tank or out in the open, not in the surge. my setup
on my one tonner runs from te standard pickup in the tank through a low pressurelift pump, which fills the surge tank, surge tank overflows back into
the main tank. the high pressure pump is mounted to the chassis where it gets good airflow and doesnt heat up much. runs through a filter then the
rail and returns back to the surge tank. the return to the surge tank goes into the top of the surge tank along with the return to the main tank so
the warm fuel is pushed prety quickly back to the main tank. never had a problem with any of it overheating or problems with power. same setup on a
lot of comp off roaders 've seen (bought the kit from a 4wd conversion mob) this system should work with any setup
sorry if i've doubled up on what others have said 
cheers
mick
|
|
Pages: 1 2 3 |